It is typical in the development of a new technology or complex system to have reliability goals. Each goal will generally be associated with a failure definition. The attainment of the various reliability goals usually involves implementing a reliability program and performing reliability tasks. These tasks will vary from program to program. A reference of common reliability tasks is MIL-STD-785B. It is widely used and readily available. Table 2.1 presents the tasks included in MIL-STD-785B.
Table 2.1 - MIL-STD-785B reliability tasks
|
Program Surveillance and Control
|
|
Design and Evaluation
|
Development
and Production Testing
|
101
|
Reliability Program Plan
|
201
|
Reliability Modeling
|
301
|
Environmental Stress Screening (ESS)
|
102
|
Monitor/Control of Subcontractors and Suppliers
|
202
|
Reliability Allocations
|
302
|
Reliability Development/Growth Test (RDGT) Program
|
103
|
Program Reviews
|
203
|
Reliability Predictions
|
303
|
Reliability Qualification Test (RQT) Program
|
104
|
Failure Reporting, Analysis and Corrective Action System (FRACAS)
|
204
|
Failure Modes, Effects and Criticality Analysis (FMECA)
|
304
|
Production Reliability Acceptance Test (PRAT) Program
|
105
|
Failure Review Board (FRB)
|
205
|
Sneak Circuit Analysis (SCA)
|
|
|
206
|
Electronic Parts/Circuit Tolerance Analysis
|
207
|
Parts Program
|
208
|
Reliability Critical Items
|
209
|
Effects of Functional Testing, Storage, Handling, Packaging, Transportation and Maintenance
|
The Program Surveillance and Control tasks (101-105) and Design and Evaluation tasks (201-209) can be combined into a group called basic reliability tasks. These are basic tasks in the sense that many of these tasks are included in a comprehensive reliability program. Of the MIL-STD-785B Development & Production Testing tasks (301-304) only the RDGT reliability growth testing task is specifically directed toward finding and correcting reliability deficiencies.
For discussion purposes, consider the reliability metric mean time between failures (MTBF). This term is used for continuous systems, as well as one shot systems. For one shot systems this metric is the mean trial or shot between failures and is equal to .
The MTBF of the prototypes immediately after the basic reliability tasks are completed is called the initial MTBF. This is a key basic reliability task output parameter. If the system is tested after the completion of the basic reliability tasks then the initial MTBF is the mean time between failures as demonstrated from actual data. The initial MTBF is the reliability achieved by the basic reliability tasks and would be the system MTBF if the reliability program were stopped after the basic reliability tasks had been completed.
The initial MTBF after the completion of the basic reliability tasks will generally be lower than the goal. If this is the case then a reliability growth program is appropriate. Formal reliability growth testing is usually conducted after the basic reliability tasks have been completed. For a system subjected to RDGT, the initial MTBF is the system reliability at the beginning of the test. The objective of the testing is to find problems, implement corrective actions and increase the initial reliability. During RDGT, failures are observed and an underlying failure mode is associated with each failure. A failure mode is defined by a problem and a cause. When a new failure mode is observed during testing, management makes a decision not to correct or to correct the failure mode in accordance with the management strategy. Failure modes that are not corrected are called A modes and failure modes that receive a corrective action are called B modes. If the corrective action is effective for a B mode, then the failure intensity for the failure mode will decrease. The effectiveness of the corrective actions is part of the overall management strategy. If the RDGT testing and corrective action process are conducted long enough, the system MTBF will grow to a mature MTBF value in which further corrective actions are very infrequent. This mature MTBF value is called the growth potential. It is a direct function of the design and management strategy. The system growth potential MTBF is the MTBF that would be attained at the end of the basic reliability tasks if all the problem failure modes were uncovered in early design and corrected in accordance with the management strategy.
In summary, the initial MTBF is the value actually achieved by the basic reliability tasks. The growth potential is the MTBF that can be attained if the test is conducted long enough with the current management strategy. See Figure 2.1.
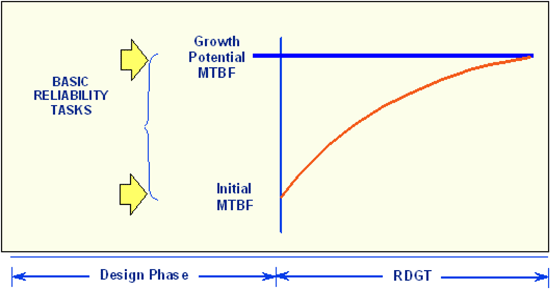
Figure 2.1: Growth potential and management strategy
|